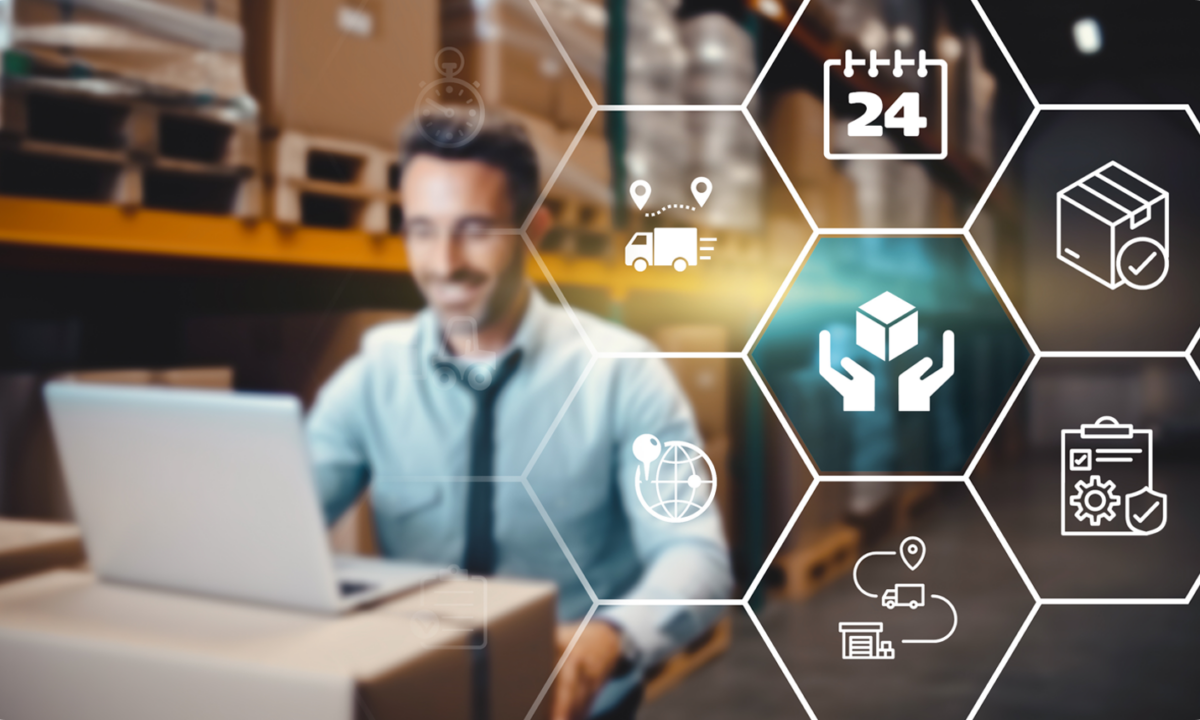
Safety Metrics That Matter: What to Track and Why
Safety in the workplace isn’t just a box to check—it’s a strategy that impacts productivity, morale, and compliance. But how do you know if your safety efforts are truly working? Tracking the right metrics provides the clarity needed to assess your current programs, identify risks, and drive continuous improvement.
Metrics are more than numbers—they’re a window into your organization’s strengths and weaknesses. The right data shows what’s working, where gaps exist, and how to make real progress. This guide explores the key safety metrics every organization should track, why they matter, and how they can build a stronger, safer culture.
Explore this Article
- Why Metrics Are Essential for Safety Management
- The Safety Metrics That Matter Most
- How Tracking Metrics Drives Improvement
- Simplifying Metric Tracking With Technology
- Conclusion
Why Metrics Are Essential for Safety Management
It’s easy to assume that safety efforts are effective simply because there hasn’t been a recent incident. But this reactive mindset leaves organizations vulnerable. Metrics allow you to move beyond assumptions and take a proactive approach.
Here’s why tracking safety metrics is critical:
- Identify Trends: Metrics uncover patterns in incidents, near-misses, and compliance gaps, providing actionable insights.
- Set Priorities: Clear data highlights where to focus your efforts, whether it’s a particular department, process, or hazard.
- Measure Success: Safety initiatives need measurable goals. Metrics show whether you’re meeting them or need to adjust.
- Improve Accountability: Transparent data ensures everyone, from frontline workers to executives, understands their role in improving safety.
Safety metrics turn vague objectives like “reduce accidents” into specific, trackable actions. They’re the foundation of a safety program that delivers real results.
The Safety Metrics That Matter Most
Tracking safety data can feel overwhelming, especially with so many variables at play. To make the process manageable, focus on these key metrics that provide the most insight into your workplace safety efforts:
1. Incident Rates: The Safety Baseline
- What It Measures: The number of workplace injuries or illnesses over a specific period, often calculated per 100 full-time employees.
- Why It Matters: Incident rates are a critical measure of workplace safety. A high rate signals systemic issues, while a declining rate indicates progress.
- How to Track: Calculate Total Recordable Incident Rate (TRIR) and compare it against industry benchmarks. Break the data down further by department or job role to identify problem areas.
Example in Action: A manufacturing company notices its TRIR is higher than the industry average. By analyzing incident reports, they discover most injuries occur during equipment maintenance. This insight leads to additional training and updated safety protocols, reducing incidents over time.

2. Near-Miss Reports: Catching Problems Early
- What It Measures: Situations where an accident was narrowly avoided, such as a worker tripping over an unsecured cable but not falling.
- Why It Matters: Near-misses provide critical warnings about potential hazards. They’re opportunities to fix problems before they cause harm.
- How to Track: Implement an easy-to-use reporting system and actively encourage workers to log near-misses. Track trends to pinpoint recurring risks.
Example in Action: A construction site logs repeated near-misses involving heavy equipment reversing in blind spots. Managers add rearview cameras and improve signage, preventing future incidents.

3. Compliance Scores: Staying Ahead of Regulations
- What It Measures: How well your organization meets regulatory safety standards and internal policies.
- Why It Matters: Falling out of compliance can lead to hefty fines, reputational damage, and operational delays. High compliance scores indicate your processes are robust and up-to-date.
- How to Track: Conduct regular audits, inspections, and reviews of safety documentation. Use safety management software to streamline compliance tracking.
Example in Action: During a routine audit, a logistics company identifies gaps in their chemical storage compliance. By updating training and implementing automated alerts for inspections, they prevent violations and maintain their safety record.

4. Training Participation and Completion: Building a Prepared Workforce
- What It Measures: The percentage of employees who have completed required safety training, as well as refresher courses.
- Why It Matters: Training ensures workers have the knowledge and skills to handle risks effectively. Low participation rates can indicate gaps in your safety program.
- How to Track: Monitor training attendance and completion rates using a learning management system (LMS). Analyze data by team or department to identify weak spots.
Example in Action: A healthcare provider notices low completion rates for fire safety training among night-shift staff. They adjust training schedules to accommodate night workers, increasing compliance and preparedness.

5. Safety Observations: Proactive Risk Management
- What It Measures: Observations conducted by managers or safety teams to evaluate workplace conditions and behaviors.
- Why It Matters: Regular safety observations catch potential hazards and reinforce accountability. They also provide insight into how well safety policies are being followed.
- How to Track: Use standardized checklists during observations and log findings in a centralized system. Look for recurring issues and track improvements over time.
Example in Action: A food processing plant conducts monthly safety observations and notices inconsistent use of PPE in certain areas. They respond by reinforcing training and updating signage, improving compliance.
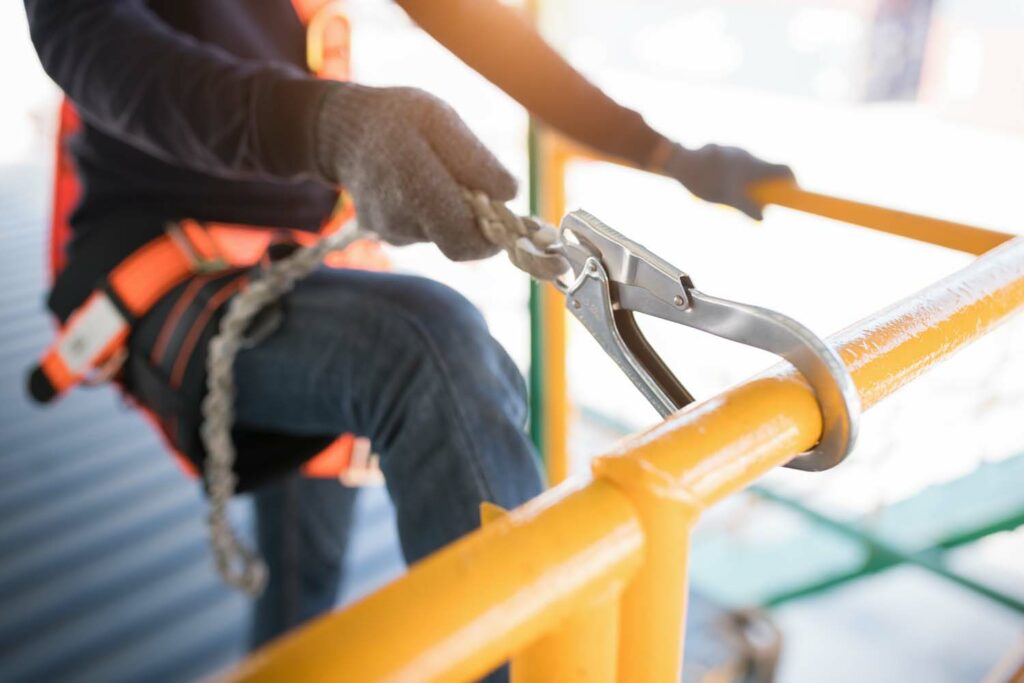
How Tracking Metrics Drives Improvement
Tracking safety metrics is only valuable if the data is used to drive meaningful change. Here’s how organizations leverage metrics for continuous improvement:
- Pinpoint High-Risk Areas
Metrics identify where hazards are most likely to occur, whether it’s a specific piece of equipment, location, or time of day. This insight allows teams to focus their efforts on areas with the greatest risk.
- Engage Workers in Safety Goals
Sharing safety metrics with employees fosters transparency and encourages participation. Workers are more likely to report hazards and follow protocols when they see how their efforts contribute to a safer workplace.
- Set and Achieve Measurable Goals
Use metrics to create specific objectives, such as reducing incident rates by 15% or increasing near-miss reporting by 25%. Clear goals drive accountability and help track progress over time.
- Measure ROI on Safety Investments
Safety metrics demonstrate the return on investment for training, equipment upgrades, and software tools. For example, a decrease in incidents can lead to lower insurance premiums and fewer operational disruptions.
Simplifying Metric Tracking With Technology
Manually tracking safety metrics can be time-consuming and prone to error. Safety management software simplifies the process by automating data collection, analysis, and reporting.
Features to Look For:
- Customizable Dashboards: View key metrics at a glance, tailored to your organization’s needs.
- Automated Alerts: Stay ahead of audits, training deadlines, and inspections with automatic reminders.
- Predictive Analytics: Use historical data to forecast risks and plan preventive measures.
The Bottom Line: Measure What Matters
Safety metrics aren’t just about numbers—they’re about creating a workplace where risks are managed, workers are supported, and operations run smoothly. By focusing on the right metrics, you can identify problems, track improvements, and build a culture where safety is a shared responsibility.
The data is already there—now it’s time to use it. Start tracking these key metrics today to take your safety program to the next level.