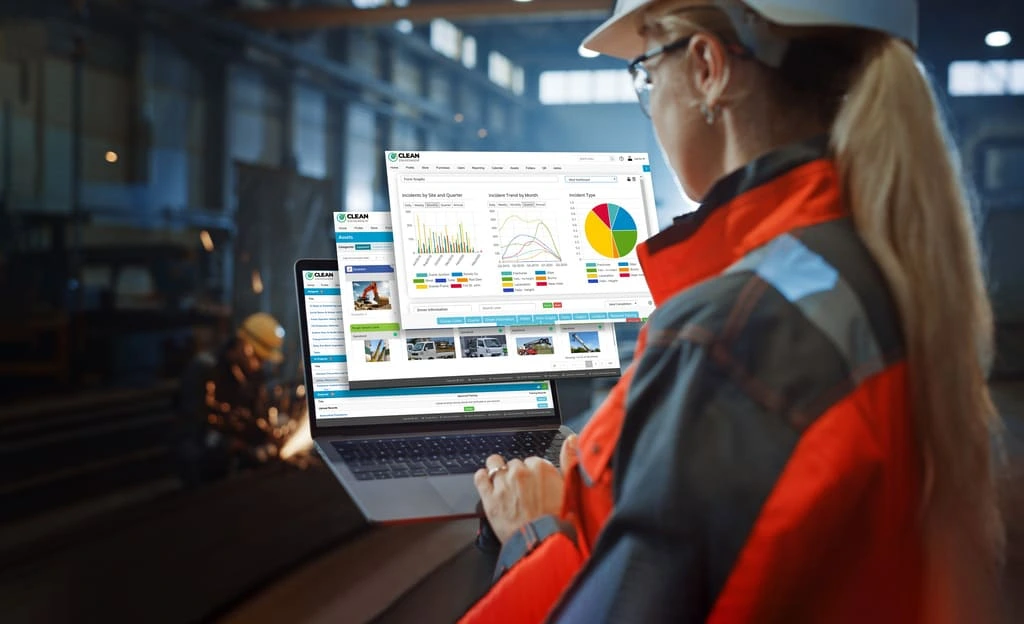
Why 6S Makes Sense for Safer US. Workplaces
In U.S. industrial settings, a clean space isn’t just nice to have—it can be the difference between a safe shift and a dangerous one. That’s where 6S steps in. Evolving from Lean’s original 5S model, 6S adds Safety as a foundational element alongside Sort, Set in Order, Shine, Standardize, and Sustain.
This approach goes beyond daily housekeeping. It creates structured routines that reduce clutter, standardize tasks, and actively prevent workplace injuries.
A Breakdown of the 6S Approach
Sort: Get rid of tools, materials, or documents you don’t need. Fewer items = fewer opportunities for mistakes and accidents.
Set in Order: Organize items where they’re needed. Tools should be easy to find, and emergency gear should always be visible.
Shine: Regular cleaning not only prevents dirt buildup—it reveals leaks, wear, and other hazards before they escalate.
Standardize: Consistency is key. Standard procedures keep teams aligned and reduce confusion on the floor.
Sustain: Keep 6S alive with regular check-ins, audits, and team involvement. Culture drives consistency.
Safety: Safety isn’t an afterthought—it’s built into each step. From tool placement to inspection routines, every action considers risk.
How 6S Benefits U.S. Companies
Integrating safety into process improvement ensures safety doesn’t live on its own island. With 6S, safety practices become daily habits, not once-a-year campaigns. That leads to fewer injuries, fewer shutdowns, and better morale.
Industries across the U.S.—from automotive plants in Michigan to logistics hubs in Texas—are seeing measurable gains in safety and efficiency thanks to this integrated system.
People Also Ask:
What is the difference between 5S and 6S?
6S includes a sixth pillar—Safety—making it more applicable for high-risk environments like construction and manufacturing.
Can 6S work in small businesses?
Yes. 6S is scalable and just as effective in small operations as in large facilities.
How do companies implement 6S?
Typically through training, visual systems, leadership buy-in, and regular audits to sustain the process.
Is 6S used in U.S. construction sites?
Yes, many contractors use 6S to reduce injuries, better organize tools, and streamline jobsite setups.
Examples of 6S in Action
- A Detroit parts manufacturer eliminated 3 common injury sources after standardizing tool storage and cleaning schedules.
- A Seattle distribution center used visual controls and 6S walk-throughs to cut incident reports by 40%.
- In Atlanta, a small electrical business used 6S to prep their shop area, resulting in quicker service calls and fewer trip hazards.
Workplace safety starts with structure. 6S provides a step-by-step way to make safety part of your culture—not just your compliance checklist.