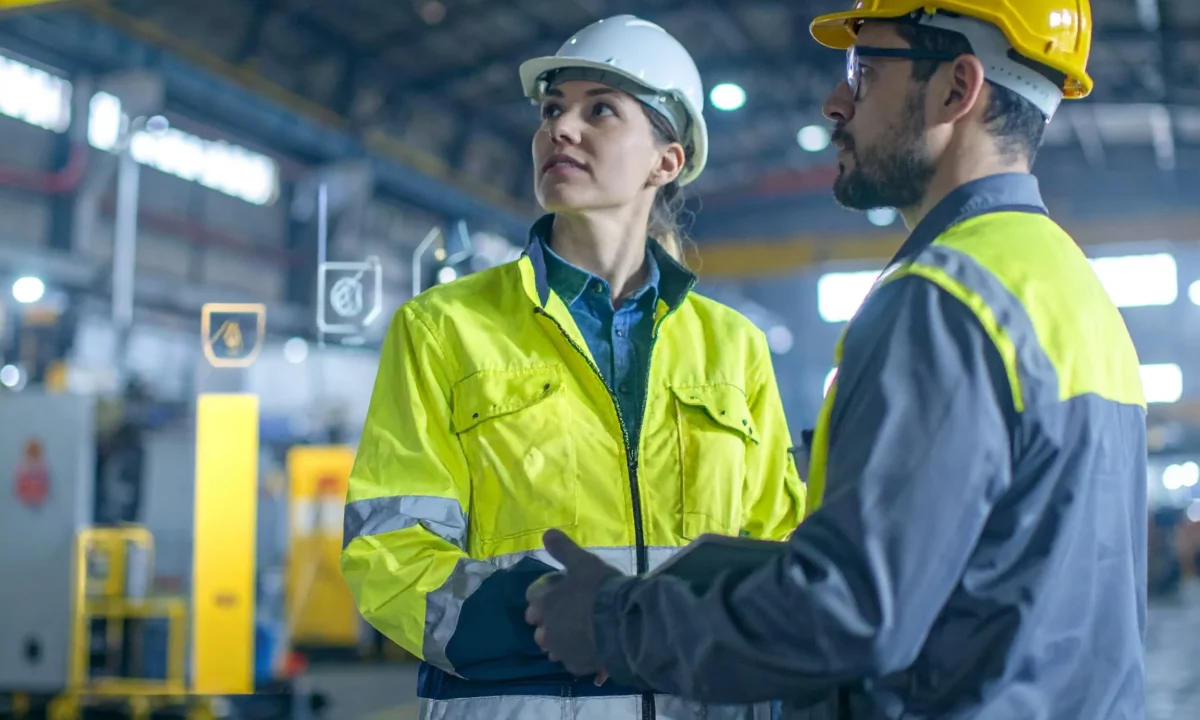
What Is Nonconformance and Why It Matters
Nonconformance happens when a product, process, or behavior doesn’t meet a required standard or expectation. Whether it’s safety-related or operational, nonconformance is a sign that something isn’t working as intended—and needs attention before it turns into a bigger issue.
When teams respond early, nonconformance becomes less of a problem and more of a performance-improvement tool.
Types of Nonconformance You Should Know
Understanding nonconformance means recognizing both its severity and impact:
- Minor Nonconformance: Small oversights or documentation errors that may not be immediately dangerous but still deviate from established practices—like an outdated label on equipment.
- Major Nonconformance: Serious failures that could cause harm or regulatory breaches—such as using machinery without proper safety checks or missing emergency systems.
The Safety Impact of Nonconformance
Nonconformance isn’t just about ticking boxes. It’s often a precursor to incidents, injuries, and costly penalties. High-functioning safety systems treat every instance of nonconformance as a learning opportunity—and a chance to fix issues before they become critical.
“Nonconformance is your system warning you in a whisper. Smart teams act before it has to shout.”
— EHS Director, Industrial Manufacturing
Spotting and Reporting Nonconformance
Strong safety cultures make it easy for workers to speak up. Use a clear and consistent system that includes:
- Routine site checks and audits
- Reports of unsafe acts or near misses
- Instant reporting through digital safety platforms
Each report should include:
- A precise issue description
- Time, location, and reporter name
- Equipment or process involved
How to Handle Nonconformance: The CAPA Method
Managing nonconformance means more than quick fixes—it means long-term solutions:
- Identify the Root Cause – Why did it happen?
- Apply Corrective Action – How will you fix it now?
- Implement Preventive Measures – How will you stop it from happening again?
Everyday Examples of Nonconformance
- Expired or missing personal protective equipment
- Incomplete or outdated safety training
- Broken fire exits or escape routes
- Unsafe chemical storage practices
- Skipping required lockout/tagout steps
Best Practices for Reducing Nonconformance
- Train regularly: Empower employees to recognize and report issues.
- Go digital: Use software to streamline reporting and track resolutions.
- Audit often: Internal reviews can catch what’s missed on the floor.
- Promote accountability: Foster a culture where speaking up is the norm—not a risk.
People Also Ask
What causes nonconformance?
Common causes include unclear procedures, poor communication, lack of training, equipment defects, and outdated documentation.
Is nonconformance the same as noncompliance?
Not always. Noncompliance refers specifically to breaking legal rules, while nonconformance includes any deviation from internal or external standards—even if not illegal.
How should you manage nonconformance during audits?
Identify the issue, document it thoroughly, perform a root cause analysis, apply corrective and preventive action (CAPA), and monitor results for closure.
Final Thought
Nonconformance isn’t failure—it’s feedback. Organizations that treat it as a warning instead of a weakness can fix problems early, protect people, and improve their systems. With the right approach, every incident becomes a step forward.
Ask yourself: Are we listening when nonconformance speaks?