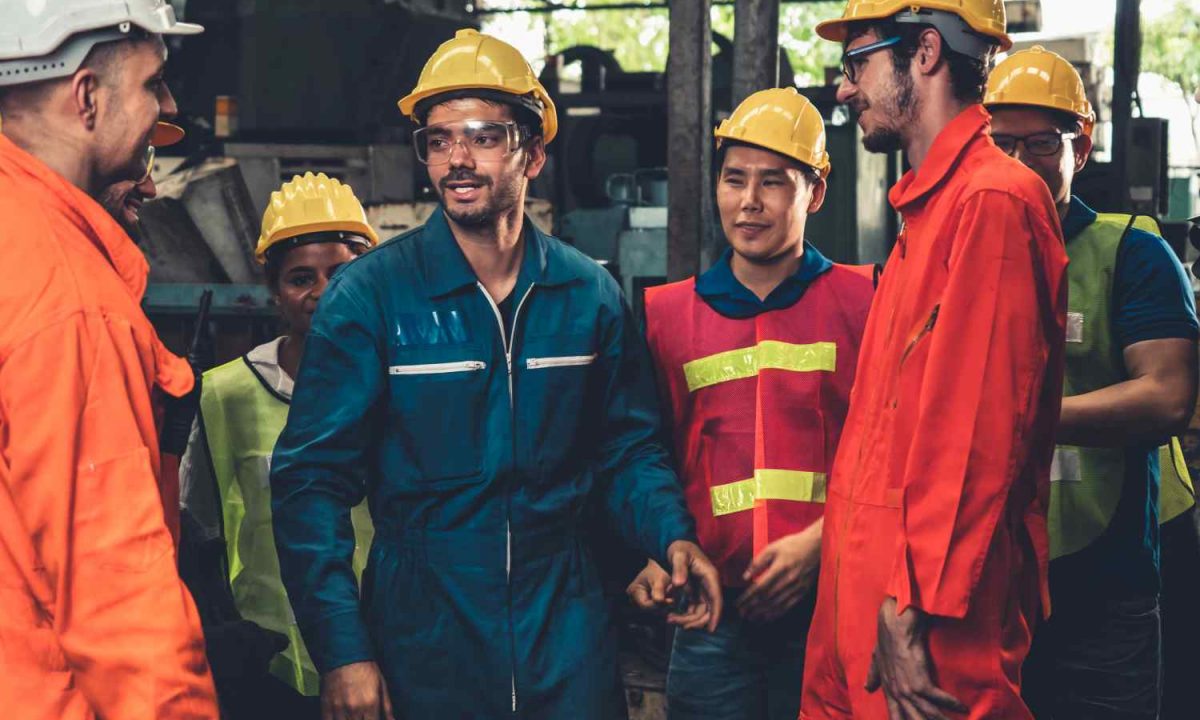
Toolbox Talks Work | 6 Tips to Improve Toolbox Talks
Toolbox talks are a simple way to decrease incidents through sharing wisdom and experience; they are sometimes also referred to as Safety Start-ups or Tailgate Meetings. In other words, a Toolbox Talk is a meeting where your staff can discuss dangers and procedures.
According to Associated Builders and Contractors, total recordable incidents dropped 78 percent with the companies that held weekly toolbox talks versus the ones who held them monthly.
These numbers are pretty staggering, yet maybe there’s more to it. With automation, compartmentalized stations, and workers being isolated in their tasks, there’s less knowledge being passed around the shop, warehouse, or construction site.
In the past, workers could converse freely and the amount of hands older jobs required meant people were closer to each other, they could share stories, techniques, and risks. Sure, there was more non-work-related banter than anything, but there was wisdom as well.
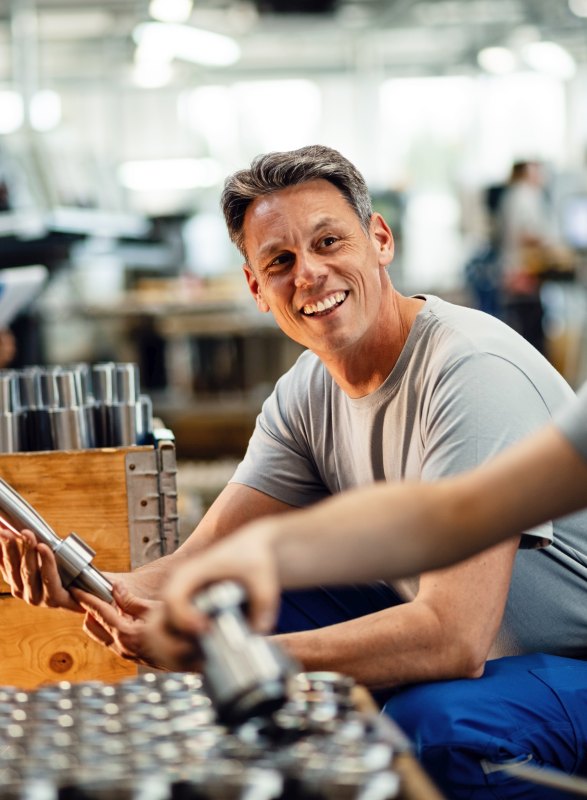
Nowadays, work is dirtier, hotter, and noisier. Likewise, it has become lonelier. With this loneliness and isolation comes a gap in knowledge. Wisdom and perspectives that would have eventually come out in the banter are now drowned out in productive 21st-century worksites. And we wonder why accidents happen so frequently. It could be due to less knowledge being passed through employees.
There’s no doubt that toolbox talks ease these modern symptoms. They give employees a focussed goal (to speak about safety) and they give staff time to share knowledge and techniques.
In short, wisdom can mitigate danger and risks. Therefore, wisdom needs a forum, or a place to spread, and toolbox talks are a good start.
6 Toolbox Tips That Foster Wisdom
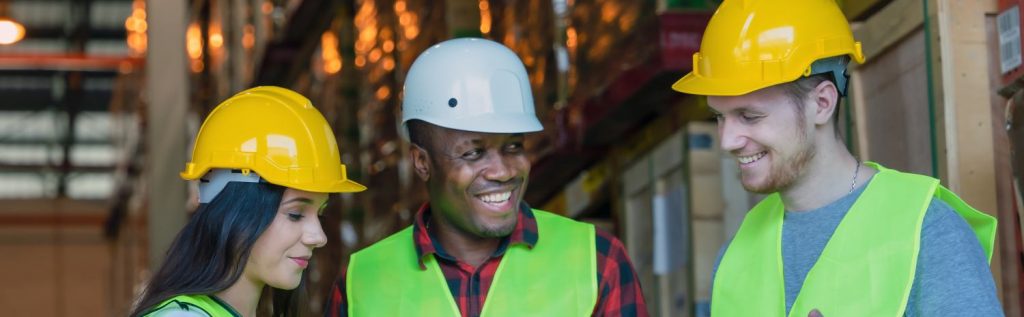
Share Stories, Not Statistics
Stories allow people to relate to conversations. They give clear perspectives and if they’re between co-workers, they share a lot in common with the listeners. Everyone has a different way of mitigating danger at work and hearing multiple stories allows people to pick and choose the techniques they’d like to adopt.
That’s why your veteran employees are your best avenue for teaching. Encourage them to share stories and perhaps even assure them that others cannot hear. Close calls happen constantly on job sites, and they can paint a bad picture for an employee who wants to keep his head down. If you assure your staff the meeting is private, it could prove more beneficial.
Focus Your Topics
Dwelling too long on certain topics won’t necessarily help teach. In fact, lengthy explanations can often bore your staff. Driving quick concise lessons into them via stories and examples is the best way to keep people interested and listening. Aids like Toolbox Talk software can help organize your topics and send useful data to other parts of your company.
Keep it Relatable
Similar to sharing stories, keeping your topic relatable is essential when speaking in these meetings. Toolbox Talks are most effective when they associate general safety lessons with the tasks the employees actually perform on a daily basis.
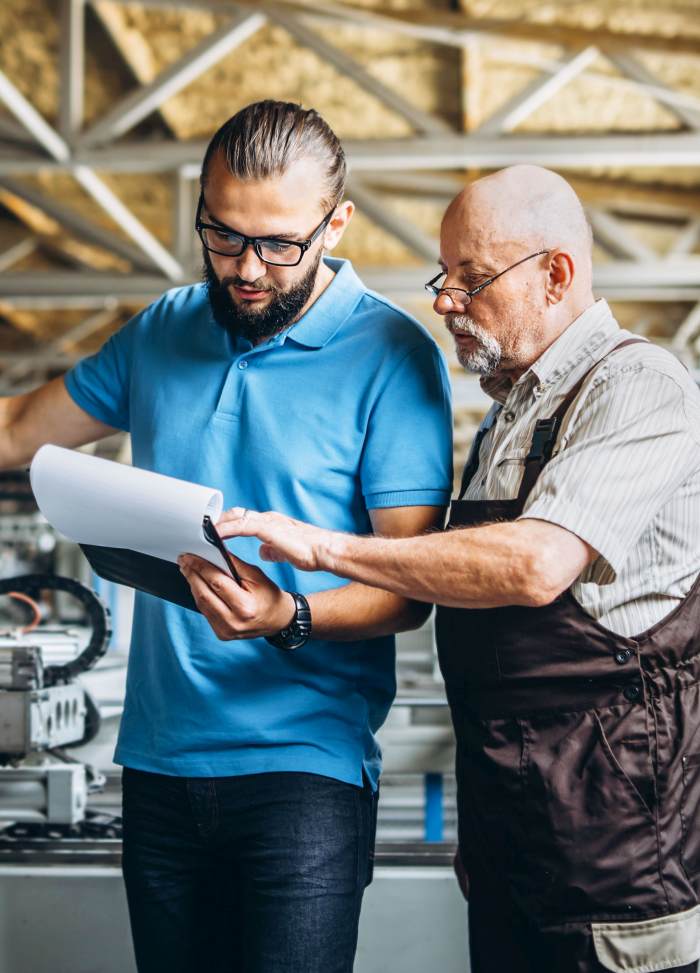
So, always use examples and stories. Like “when using this lathe, never wear loose clothing due to the rotating parts and the danger of winding.”
Use Props and Places
Some of the best professors in the world use symbols and props to keep their class interested. This helps with visual learners and other different styles of learning that are often overlooked in traditional settings. It also breaks up the monotony.
So if you’re speaking about a tool, bring it out. And if you’re speaking about a place you can’t move, bring the toolbox talk to the setting.
Use Timing to Your Advantage
Change times like you changed locations and props to get the most out of your safety meetings. Ask your staff for their opinions as well. Some people learn better in the morning, others after they’ve woken up. Some companies have had great success holding meetings after lunch so the employees can share close calls or near misses they had in the morning.
Use an Optimistic Tone
You don’t want to instill dread or fear in your staff. A better approach is to keep the conversation optimistic and positive.
When speaking about lockout procedures, focus on their benefits. For instance: “Now that the person working on the machine has the only keys to the locked-out equipment, they can be sure there is no chance they will be harmed in an unscheduled start-up.”
Conclusion
Toolbox Talks can not only mitigate incidents and accidents, but they can share wisdom and increase productivity. Employers who see toolbox talks as just lost production time deny their employees one of the greatest teachers in nature, elder experience.
Written by Jordan Kovacsik – BIS team member, author, and safety enthusiast who worked in the steel industry for a decade.