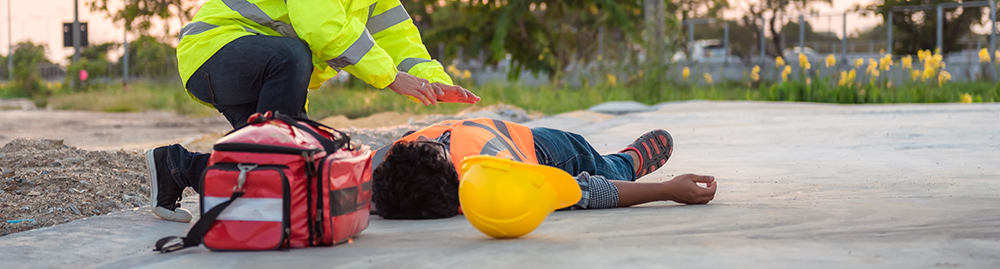
How to Avoid the 5 Most Common Workplace Injuries
The US Bureau of Labor Statistics reported 5,250 fatal workplace injuries in 2018, the latest year with available data. This means that 14 or 15 Americans lose their lives at work each day, on average. Many of these accidents can be prevented when workers receive continuous safety training, and their employers provide all the information and equipment necessary to stay safe.
In total, 2,834,500 nonfatal injuries and work-related illnesses were reported for 2018, and 900,400 involved days away from work. The following were some of the most common workplace injuries:
- Sprains, strains and tears: 308,630
- Back injuries, including spinal cord injuries: 142,230
- Falls, slips and trips: 240,160
Online safety training can be very useful for your company, as a way to keep your employees updated with the latest safety procedures, technologies, and regulations. This article provides an overview of five common workplace injuries, and recommendations to prevent them.
1) Cuts or Punctures
There are many causes of cuts and punctures on worksites, but these injuries most often occur when sharp tools are not used properly. The risk of these injuries is reduced when workers are trained on how to use tools correctly, and the proper use of personal protective equipment (PPE).
While many cuts and punctures only damage the skin, in severe cases they may pierce muscles, tendons, ligaments, organs, and bones. Medical attention is critical since these wounds are very vulnerable to infection. Further complications of these injuries can include tetanus or lockjaw, which is often deadly.
2) Poisoning
While common sense tells us to avoid toxic substances, there are situations where exposure is likely if companies are not careful. Consider the following examples:
- Some toxic chemicals are gases or liquids that evaporate quickly. In these cases, poisoning may occur by inhaling the substance. The risk is even higher when dealing with odorless and colorless gases, such as carbon monoxide.
- Toxic substances may also be ingested accidentally. For example, a clear and odorless liquid could be confused with drinking water.
The OSHA Hazard Communication Standard was first implemented in 1983 to identify hazardous chemicals in the workplace. It was expanded to all industry sectors in 1987, and OSHA implemented the United Nations Globally Harmonized System (GHS) in 2009. You can reduce the risk of exposure by ensuring your employees are trained on how dangerous materials are labeled and what PPE or equipment is required.
3) Sprains or Strains
While these two terms are often viewed as synonyms, they are different from a medical standpoint. Both types of injury involve tearing or overstretching of tissue, but a sprain affects ligaments, while a strain affects muscles or tendons. Many of these injuries occur when workers exert high forces, such as when they carry heavy loads. There are many ways in which companies can reduce the risk of sprains or strains at work:
- Arranging the workplace in a layout that minimizes distances where employees exert themselves physically.
- Implementing load standards to reduce employees from overexerting themselves.
- Regularly inspecting tools and lifting equipment, to ensure they are in good condition.
- Online training on preventing sprains and strains, covering situations where these injuries are likely, and how workers can protect themselves.
Like many other worksite accidents, these injuries can be avoided with the right information and equipment. Promoting a culture of safety is valuable technique to ensure procedures and protection measures are understood, and followed, by all employees.
4) Broken or Fractured Bones
Traumatic injuries like falling from height often cause a bone fracture, and minor fractures can also occur from repetitive efforts. As skeletal tissue deteriorates with age, companies that employ seniors must be especially careful since these employees are more vulnerable to breaking bones.
Bone fractures can also be minimized with training on key topics such as:
- Fall protection
- Ladder safety
- Working at height
- Safe use of equipment
In addition to being very painful, fractures can cause permanent disability in severe cases. Protecting employees from harm is the ethical and socially responsible thing to do, but also beneficial for productivity.
5) Burns, Scalds, or Chemical BurnsÂ
Poisoning is not the only substance hazard in workplaces. There may also be hot surfaces and liquids, or chemicals that cause damage with contact alone. The GHS also covers hazards like these, and exposure is less likely when materials are properly labelled.
Of course, adequate PPE and safety protocols are also important when there are any hazards that can cause burning or scalding. For example, if a process uses a strong acid, the container should only be handled if closed properly and the appropriate PPE is worn.
Conclusion
Companies are responsible for creating safer work environments, and they should ensure that workers have all the knowledge and equipment needed to avoid hazards.
Awareness is fundamental for accident prevention, and online safety training can teach your employees about workplace hazards. Accidents are much less likely when a company places safety first, providing its employees with everything they need for prevention.